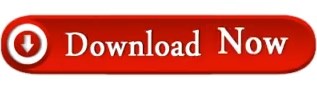
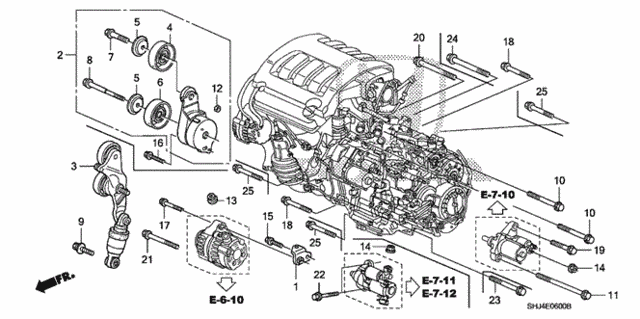
click to load Disqus comments for this story This enables Disqus, Inc. Check out the deal on Insane Shafts 1000HP Axle (RHR) - Honda NSX W/ K-Swap 91-05 at Evasive Motorsports. The simple logic is that the ECU was designed for use in an 02-04 RSX, so if you follow the RSX wiring it will work. The kit comes with three mounts and options of 75A, 85A, and 95A bushings.
#2008 honda accord 3.5 alternator bracket code
DOCTRONIC IMMOBILIZER K-SWAP MOTORSWAP (CIVIC/CRX/DEL SOL/INTEGRA) of the Multiplexer CEL (Honda Code 39 or OBD2 P0600), too. O2 primary sensor wired to suit PRA narrow band logic. Had to end up installing a Helicoil to properly repair - because of very limited access - not the easiest repair.Nsx k swap wiring Original ECU. I know now to support the alternator with one hand, while threading this bolt with my other fingers.
#2008 honda accord 3.5 alternator bracket full
The heavy alternator and the full weight on this lower bolt makes it difficult to start by hand. I know - I am rather careful with my shadetree mechanic ability, but I cross threaded this lower bolt during an alternator replacement. So the proper range is narrow - needs to be tight enough to eliminate alternator vibration, yet not too tight to damage the threads.
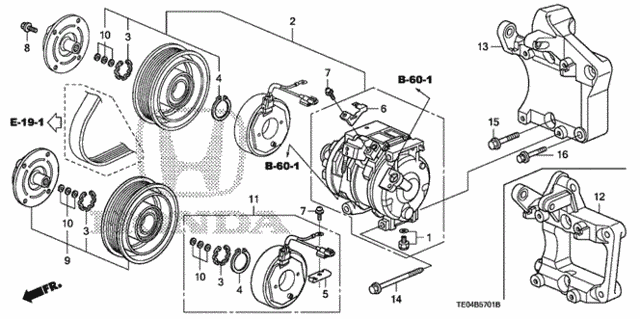
The aluminum threads are soft and the long M10 x 1.25 bolt can easily damage the threads if overtorqued. If you had your alternator replaced, it is easy to cross-thread this bolt during installation - the torque spec here is critical. This bolt should be torqued to 33 ft-lbs to be able to hold the alternator firm and reduce the vibration that weakens the bracket.
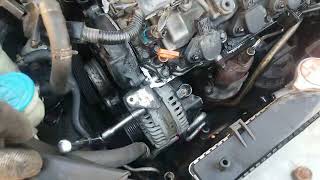
I read this in an internal Honda-Tech bulletin. The problem with the constant alternator bracket ("stay") breaking is most likely from an improperly torqued lower alternator bolt. One nice thing about this is that if your homemade part ever did break, you could fix it with your own tools and leftover angle iron from before in less than an hour. Your friendly hardware store should be able to match the bolts you removed with the right size drills and taps. Just be sure to only get the glue on the part of the nut that needs to be attached. Actually, with just a little more equipment - a good hacksaw or power metal saw, a piece of 1/4 inch x 1 inch x 2 inches long regular angle iron, an electric drill with the right size bits and a tap for each hole, I could make one that I do not believe would break ever!! I would attach an additional nut on the back side of the two alternator side holes. I logged in to the forum to find replacement part cost, but now that I see it is a regular problem, I may Superglue the old one and take it to a machine shop and have a new one made of heavy angle-iron steel. I noticed the broken ends on the block side and took off the plastic cover. Without damaging my new belt, I began checking for alternative problems. The belt came off right after the problem was discovered or I might have saved the expense of a tensioner assembly and possibly of the belt, but after I replaced everything properly I discovered I had done nothing to resolve the problem. Because the plastic rain and dust shield over the sparkplug area, that problem was not obvious. After 90,000 miles on her 2003 Honda Odyssey LX, the upper alternator mounting bracket broke.
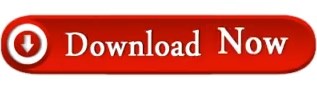